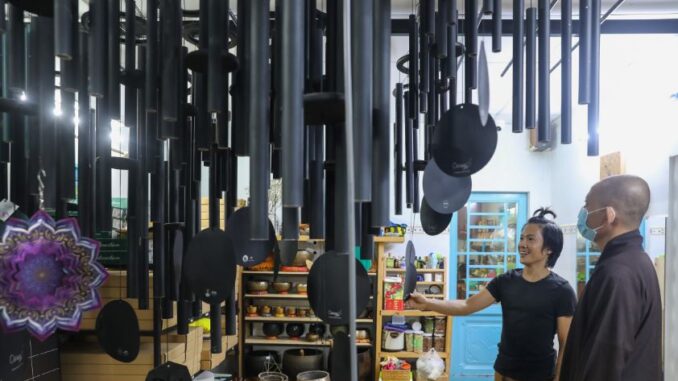
HO CHI MINH CITY – The Zen music wind chimes factory of Mr. Hong Duc, 34 years old, produces 300 products per day, selling price up to 12 million VND per set.

Mr. Tran Ngoc Hong Duc from Binh Quoi, Binh Thanh District, has been manufacturing and trading meditation music wind chimes since 2012. This is a type of bell that emits sound at a frequency of 432 Hz, which is said to be a natural healing frequency. However, very good for health.

Before coming to this art form, Mr. Duc was an information technology engineer. In 2012, during a visit to Chon Khong Monastery (Ba Ria – Vung Tau), he suddenly “fallen in love” with the sound coming from the large wind chimes in the main hall.

After that time, he researched and started researching and manufacturing this type of wind chimes. “I also failed many times, had to give up a lot of products,” Duc confided.
Currently, he has a factory of about 400 m2, with 5 regular employees.

In 2017, Mr. Duc quit his job in information technology and dedicated himself to making wind chimes.
Materials for making bells are aluminum tubes, powder coated, of all sizes, with a length of about 3.3 m and a thickness of 15 to 60 mm.

According to Mr. Duc, the stage of cutting the aluminum tubes and then drilling holes to pierce the wire is very important. People cutting and drilling not only have to do the right technique but also have to be able to perceive sound.
“Precise cutting will produce the correct frequency when harmonizing, drilling the right dead point of the tube will not affect the sound. Each bell, just a little different, will immediately sound different,” said the owner of the workshop.

The aluminum tubes after cutting are folded and sonicated with a spoon.

After cutting and sounding, the pipe ends are smoothed, rounded and cleaned inside. This work also needs the meticulousness of the worker, because only a small scratch in the tube will also make the sound “distorted”.

Employees threaded wires into the holes to connect the tubes together, creating a wind chime shape. On average, each product takes 2 to 3 tubes of material.

In the yard, Mr. Tri, a factory worker, paints the products, filling the scratches during the processing. “I worked here for 3 months, found this job quite interesting. Making a bell is not only good skill but also has to know the perception of sound, be careful and honest because everything is processed by hand, with one small step wrong. neither,” Tri said.

Each wind chime costs from 400,000 VND to 12 million VND. During peak periods, the factory produces more than 300 sets of bells per day.

When not at the factory, Mr. Duc designs new products to meet the tastes and needs of customers.

In the living room, he also displays a collection of more than 20 types of bells from Vietnam and many other countries, including products that must be auctioned abroad.

Visitors to buy bells are usually people who practice meditation, monks, pagodas, etc. Many people also come to learn about music therapy, usage and cultural values of bells.
Before the epidemic, Duc sold nearly 1,000 wind chimes every month. Follow vnexpress